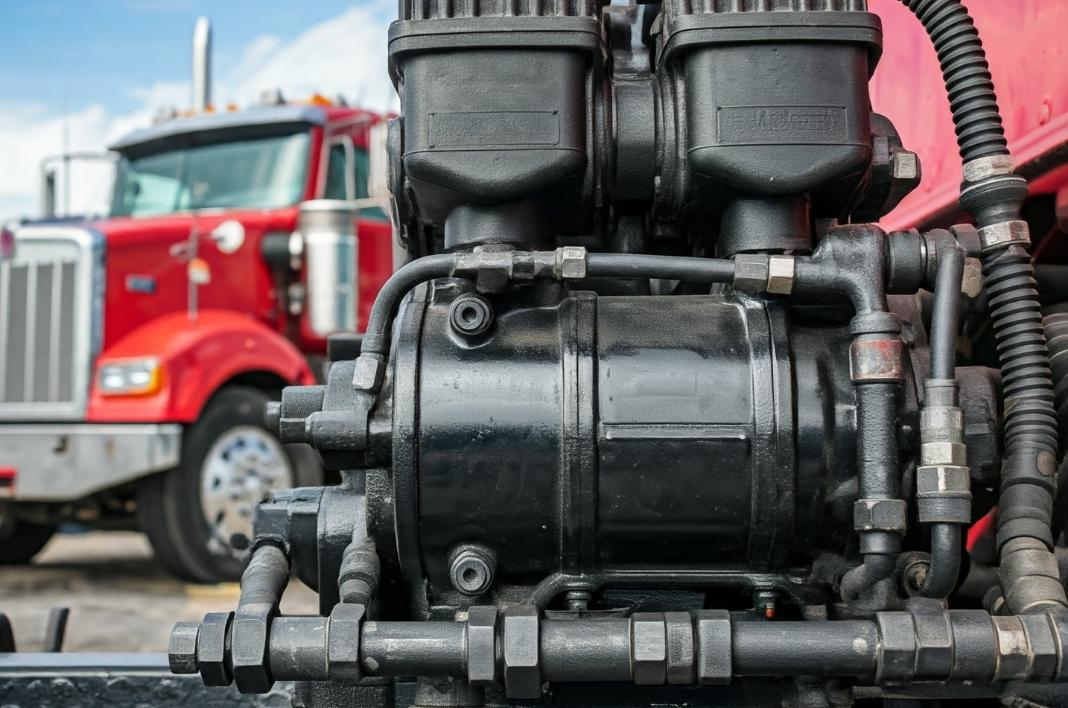
Air compressors are crucial components in many heavy-duty trucks, particularly for air brake systems. Given their central role in ensuring safety and functionality, it is imperative to maintain them properly. At TORQUE PARTS, we understand that routine maintenance of air compressors not only enhances their efficiency but also prolongs their lifespan. In this article, we will provide a comprehensive step-by-step guide to maintaining air compressors, highlight the necessity of regular oil changes, filter replacements, and belt inspections, and offer advice on troubleshooting common issues.
Importance of Regular MaintenanceAir compressors power the air brake systems that keep trucks safe on the road. A malfunctioning air compressor can lead to brake failure, compromising the safety of both the driver and others on the road. Regular maintenance is essential to keep the compressor functioning well, which makes preventive care not just beneficial but essential.
Step-by-Step Guide to Air Compressor Maintenance
To ensure your air compressor operates optimally, follow this step-by-step maintenance guide:
Step 1: Daily Visual Inspections
Start with a daily visual inspection of the air compressor. Check for any leaks, peculiar noises, or unusual vibrations. Inspect hoses and fittings for signs of wear or damage. Ensuring that the compressor is clean can help spot any issues before they escalate.
Step 2: Oil Level Check
Oil lubricates the internal components of the air compressor, preventing wear and tear. Check the oil levels regularly:
- Frequency: Perform this check at the beginning of each shift or at least once a week.
- Procedure: Use the manufacturer’s dipstick or gauge to verify the oil level. If it’s low, top it up with the recommended oil type.
Step 3: Oil Changes
Regular oil changes are critical for optimal compressor function:
- Interval: Generally, oil should be changed every 500 to 1,000 hours of operation, but always consult the manufacturer’s guidelines.
- Procedure: Drain the old oil while the compressor is warm (this will help in easier removal). Replace with high-quality oil recommended by the manufacturer. Remember to dispose of old oil responsibly.
Step 4: Filter Replacements
Filters play a crucial role in protecting the air compressor from contaminants:
- Types: Replace air filters, oil filters, and separator filters as recommended by the manufacturer.
- Frequency: Typically, air filters should be replaced every 3 to 6 months, but this may vary based on usage and operating conditions.
- Procedure: Follow the manufacturer’s instructions for replacing each type of filter. Ensure that seals are in place to prevent leaks.
Step 5: Belt Inspections
If the air compressor uses a belt drive system, ensure the belts are in good condition:
- Frequency: Inspect belts every month for signs of wear or cracking.
- Procedure: Check for proper tension. The belt should not be too tight or too loose; if it is, adjust accordingly or replace the belt if worn out.
Step 6: Drain Moisture
Moisture accumulation in the air tank can lead to corrosion and decreases the efficiency of air delivery:
- Procedure: Drain the moisture from the tank daily. Open the drain valve and let the moisture escape until only air comes out. This is especially crucial in humid conditions.
Step 7: Electrical Connections Check
Ensure that all electrical connections are secure and in good condition:
- Procedure: Inspect wires for fraying, corrosion, or loose connections. Repair or replace connections as necessary to safeguard against electrical failures.
Troubleshooting Common Air Compressor Issues
Even with regular maintenance, air compressors can encounter issues. Here are some common problems and troubleshooting tips:
Low Air Pressure
If the air compressor fails to deliver sufficient air pressure, it may be due to:
- Causes: Possible leaks in the air lines or a faulty pressure switch.
- Solution: Inspect all connections for leaks using soapy water. Replace faulty components as needed.
Unusual Noises
Unusual noises may indicate mechanical problems:
- Causes: Worn bearings, loose components, or metal-to-metal contact.
- Solution: Shut down the compressor immediately, inspect internal components, and repair or replace parts as necessary.
Excessive Vibration
Vibrations can be a sign of imbalanced components:
- Causes: Misalignment of the motor and compressor, or a damaged mounting.
- Solution: Check for proper alignment and secure all mounting bolts tightly. If a part is damaged, replace it as required.
Overheating
An overheating air compressor is a significant concern:
- Causes: Insufficient oil, dirty filters, or blocked air intake.
- Solution: Immediately turn off the unit. Check the oil level and add oil if necessary. Clean or replace filters to ensure adequate airflow.
At TORQUE PARTS, we understand how vital air compressors are to the overall performance of American trucks, particularly in air brake systems. Following a diligent maintenance routine can significantly extend the lifespan of your air compressor, ensuring that your truck remains safe and reliable on the road. Regular oil changes, filter replacements, and belt inspections are crucial elements in this process. By being proactive and addressing potential issues early, you can avoid more significant problems down the road—ultimately saving time and money.
Remember, a well-maintained air compressor is not just an operational necessity; it is a key component that contributes to the safety and performance of your vehicle. Prioritizing maintenance today can lead to safer journeys tomorrow.
Follow us to get detailed information: Air Compressors
Check out our Air Brake Components